Inductors are used across many industries to store energy, regulate the flow of current, and create impedance. Circuits require different types of inductors as well as core and winding styles to perform optimally in a given application. Understanding inductor properties is the best way to determine which materials and shapes are best suited for your custom needs. This blog post will discuss the properties of inductors and design factors to consider before deciding on a particular product.
Types of Inductor Materials
An inductor’s material is customizable to address specific power requirements and other needs.
The most common core materials for inductors include but are not limited to:
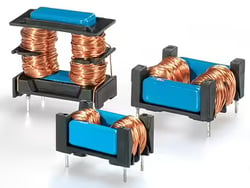
- Air core inductors: Also known as ceramic core inductors, air core inductors feature a very low thermal coefficient of expansion, delivering high inductance stability. Air core inductors are non-magnetic, so there is no permeability value increase.
- Ferrite core inductors: As a crystalline magnetic material of iron oxide and other elements, ferrite core inductors feature high electrical resistivity and high magnetic permeability. Ferrite cores are classified into soft ferrite and hard ferrite core inductors, depending on their magnetic coercivity.
- Iron core inductors: This type of core material features high power and inductance values but has limited high-frequency capacities. They are a good choice in applications requiring low-space inductors.
- Iron powder core inductors: Featuring a higher resistivity than silicon steel, iron powder cores are composed of specially processed iron particles mixed with a binder material, such as epoxy or phenolic. The core is then pressed and baked into their desired final shape. This type of core material is useful when core loss must be considered.
- Silicon steel core inductors: This material is easily formable and relatively inexpensive. It features low resistivity, allowing it to readily conduct an electrical current. This means that undesirable eddy currents are able to flow into the core material.
The Different Inductor Shapes
Like the material, the inductor’s shape can also impact its properties and compatible applications. Each inductor core shape offers varying benefits and drawbacks. Some common inductor shapes include:
- “C” core: Also known as cut core or tape wound cut core, this shape is ideal for applications requiring a large number of transformers in non-standard lamination sizes.
- “E” core: Less expensive than other shapes, “E” cores feature a simple bobbin winding and are easy to assemble.
- Laminated core inductor: These are made of thin, laminated steel sheets, which help block eddy currents and minimize energy loss.
- Toroidal inductor: Typically made of materials like ferrite or powdered iron, this shape looks like a donut or ring of wound wire. They are primarily used in medical devices, air conditioners, telecommunications devices, and refrigerators.
- “U” core: Ideal for high-power applications within a tight space, the “U” core has legs in the shape of a “U” to support superior voltage isolation and low leakage inductance.
Inductor Applications
Inductors are used for many purposes, such as blocking, choking, and filtering high-frequency noise in electrical circuits. They are also used in common-mode chokes and dual-mode chokes, as demonstrated in this video. Inductors store and transfer energy in power converters, serve as sensors and transformers, and act as complex loading devices and transient suppression chokes.
Below are common applications of inductors in certain industries:
- Audio and sound processing: automotive stereo systems, line and noise filters, handheld audio systems, soundbars, portable docking stations
- Industrial and commercial equipment: battery-powered devices, industrial controllers, TV and radio receivers, switching regulators
- Medical equipment: CTs, endoscopes, dialysis machines, MRIs, ultrasound diagnostic equipment, x-ray panels
Considerations for Inductor Design
To ensure optimal performance and longevity, three important factors should be taken into account when designing an inductor: core material, wire and winding, and packaging.
Core Material
Inductor materials must effectively meet an application’s unique circuit requirements. While some materials can store large amounts of energy at DC or low frequencies, for instance, they will exhibit high losses at high frequencies. Regardless of the rest of the design, an inductor with an ill-suited core will not perform to its potential.
Core material type determines properties such as energy loss and storage, inductance, and stability. Depending on the requirements of a given application, materials such as silicon steel, nickel, iron, ferrite, or another material can be selected.
Wire & Winding
Wire and winding—how the wire is wound around the core—are the most important considerations during the design stage, as they affect every measurable inductor property. Wire material, size, shape, winding frequency, and pattern should all be carefully chosen. The inductor winding design determines the coil losses.
Packaging
Packaging must also be considered—not the materials an inductor is shipped in, but rather the material in which it is sealed. Environmental factors are usually the most pressing concern here. For optimal protection, inductors must be properly hermetically sealed or encapsulated (or even encased in metal, depending on the application). Mechanical stresses like shock and vibration as well as ambient temperature and humidity all determine the best package.
Inductors From Triad Magnetics
Inductors must be designed according to the needs of each application and carefully packaged to withstand the demands of their end-use environments. Triad Magnetics manufactures industry-leading inductors, backed by over 75 years of experience. We offer custom design, prototyping, and testing services from our ISO 9001:2015-certified facility.
For an in-depth explanation of inductor design and all its related aspects, download our eBook, “Understanding Inductors” If you have any questions about our products and services, contact us. You can get started on your next project by requesting a quote today.